Manufacturing and value-chain activities—opportunities and challenges
Introduction
4.1
This chapter focuses on the opportunities and challenges associated with
electric vehicle (EV) manufacturing and value-chain activities including:
-
EV and EV component manufacturing;
-
Battery manufacturing and commodity value-adding; and
-
Charging infrastructure.
EV and EV component manufacturing
4.2
The Committee has heard about the future opportunities for manufacturing
in the industries related to EVs. A number of companies the Committee has
spoken to and visited are already on the front foot seeking to take advantage
of the commercial opportunities presented by the rising consumer demand for
EVs.
4.3
In its submission, Deakin University shared its positive outlook for manufacturing
in this area:
No component, nor assembly of a complete electric vehicle, is
beyond the capability of Australian industry.
The opportunities for local manufacture will, therefore, be
determined on price, production volumes and access to requisite designs, which
may otherwise be constrained by intellectual property protections.
Volume can be enhanced by exports and intellectual property
issues addressed through partnerships. A comprehensive analysis of supply chain
requirements and opportunities should be undertaken by an industry capability
network or similar agency.[1]
4.4
One of the inherent benefits to EVs is that they are less complex than
internal combustion engine vehicles and hence have 'thousands of fewer
components per vehicle'.[2]
Not only does this lead to potentially lower costs per vehicle (excluding the
batteries) for the consumer (and cheaper servicing), but it also reduces the capital
cost and complexity of manufacturing including logistics.[3]
4.5
There will also be changes to how motor vehicles are made and how much
they cost to build. Uniti Australia has stated that 'new advanced manufacturing
processes, light-weight materials and new vehicle designs have led to a
dramatic reduction in the costs of assembling vehicles'.[4]
Dr Brett Dale, Chief Executive Officer of the Motor Trades Association of
Queensland (MTAQ) made his views clear on the future of manufacturing,
including custom order motor vehicles:
I [spoke about] the concept of 3D printing. With the way in
which that's developing and the rate at which it's developing, there's a real
possibility that, in the next five to 10 years, you'll custom print the car that
you want. When you look at the components associated with electric vehicles,
there are way fewer than the existing fleets on the road. Printing a fully
electric vehicle, which will be autonomous by then, could be done custom; you
would get a product comparative to an architecturally designed home or a spec
home. So, manufacturing is the key, and governments need to support the
investment into that, because it will be the technology that determines whether
we are a competitive nation.[5]
4.6
The advent of automated vehicles will also likely present changes to structural
and material requirements, and vehicle design, 'which might create further
opportunities to utilise Australian resources'.[6]
4.7
Although the majority of submitters and witnesses expressed support for
local manufacturing associated with EVs, others, such as Mr Tony Weber, Chief
Executive Officer of the Federal Chamber of Automotive Industries were more
circumspect:
On the question of manufacturing in the future, obviously we
ceased [vehicle] manufacturing late last year [2017]. In the future, if we were
to look at manufacturing being realistic, we'd have to examine the fact that,
despite Australia having a market of 1.2 million vehicles a year, no vehicle
sells at 50,000 units per year in Australia. Fifty thousand units is not
considered to be the scale required for a factory anywhere in the world, and
therefore you would need extensive export markets, in conjunction with a very
successful product in the domestic market, before it was viable. One of the
substantial issues with manufacturing in Australia is lack of real access to
markets outside of Australia, especially in the Asian region, because of
tariffs and non-tariff barriers.[7]
Residual car-making skills and
experience
4.8
In October 2017, the General Motors (GM) Holden automotive manufacturing
facility in Elizabeth, South Australia was closed. As the last car making plant
in Australia at the time, it also signified the end of passenger vehicle manufacturing
in Australia at that time.[8]
This left not only hundreds of highly skilled automotive workers unemployed,
but many thousands more who worked in businesses supplying components to GM
Holden. This effect has been mirrored across the country in the wake of other
high profile car plant closures in recent years with estimates suggesting that
up to 50 000 workers could have been impacted as a result.[9]
The Committee notes that Iveco manufactures trucks at its Dandenong plant.[10]
4.9
Notwithstanding the closure of Toyota's Altona plant in western
Melbourne, the Hobsons Bay Council observed that 'there remains capacity and
expertise in the areas of vehicle design, heavy vehicle manufacturing,
conversions, component manufacturing and servicing'. This capacity stands ready
to take advantage of the growth in EVs.[11]
The South Australian Government put forward a similar view:
The state also retains an automotive sector following the
closure of Holden with many component suppliers, a strong research base and a
remnant pool of skilled workers.[12]
4.10
The Victorian Automobile Chamber of Commerce (VACC) expressed its view
that opportunities exist for Australian industry stemming from a ready skilled
workforce and the introduction of automated manufacturing techniques:
Whilst passenger car manufacturing has now ceased, it is not
beyond possibility that the assembly of EVs may become a viable business
option. EVs have fewer components than traditional ICE vehicles, thus
eliminating the need for many costly manufacturing processes such as engine
casting, tooling and the creation of component parts. Given the inherent
residual engineering capacity that is available in Victoria and other states,
business models involving the importation of electric motors and the assembly
of EVs from Completely Knocked Down packs (CKDs) using robotics and other
automated processes may be viable.[13]
4.11
The Australian Council of Trade Unions (ACTU) has argued that it would
make sense to take advantage of such a large skilled workforce and existing
supplier capacity, and situate any new industry in areas where skilled
automotive workers and associated businesses are located:
EV manufacturing could be centred in precisely the
communities and area, such as Elizabeth in SA and Geelong in Victoria, that
have been most affected by the destruction of the Australian car industry. The
return of vehicle production to these areas would revitalise these communities,
bringing jobs, allowing families to escape and poverty and would encourage the
engagement of young people with education and training.[14]
4.12
The Australian Manufacturers Workers Union (AMWU) echoed these
sentiments:
Australia is uniquely placed as a country with a ready supply
of skilled workers capable of building a world-class EV manufacturing facility.
As a result of the closure of Australia's conventional automotive manufacturing
industry, there are many workers capable of supporting the development of an
electric vehicle industry in Australia.
In addition, there is also a significant infrastructure to
support the development of such an industry in Australia, particularly in the
former regions that hosted automotive manufacturing facilities until recently.
These areas have vocational education providers that specialise in the skills
required, they have connections for import and export and are close to
established supply chains.[15]
Automotive Transformation Scheme
4.13
As car manufacturers signalled their intention to close Australian
manufacturing facilities, the Australian Government established a $2 billion
industry adjustment scheme called the Automotive Transformation Scheme (ATS).
The ATS, started in 2011 will run until the end of 2020, and provides:
businesses
involved in the Australian automotive industry with cash payments to cover up
to 15% of the cost of investing in plant and equipment, and 50% of the cost of
investing in research and development, to encourage investment and innovation
in the Australian automotive industry.[16]
4.14
The ATS has been taken up by firms such as Precision Components to
reshape their businesses for the opportunities of the future. Mr Christian Reynolds,
Director of Precision Buses, a South Australian bus manufacturer, explained his
company's journey from 'metal stamping component manufacturer' to an 'advanced
manufacturing group'.[17]
Precision Buses is a genesis from Precision Components.
Precision Components was a component manufacturer at tier 1 level to Holden and
Ford, which, through the Automotive Transformation Scheme, took the opportunity
to transition into vehicle manufacturing. We've set up an advanced
manufacturing facility in Edinburgh Parks [South Australia], where we have a
level of collaboration between four business entities. We're looking at
co-locating to advance the knowledge share and the engineering detail around
how we progress autonomous and electric vehicles.[18]
4.15
The Committee heard that there were a number of limitations with the ATS and
its eligibility requirements. For example, many companies do not meet the
minimum throughput of 30 000 vehicles per annum. However, there is an
exemption in the form of a national interest test. The Department of Industry,
Innovation and Science's (DIIS) submission explained how the ATS was being
expanded:
Businesses that have made a financial commitment to carry on
business in Australia as a motor vehicle producer or supplier to the automotive
industry, for the first time can also participate in the scheme. Businesses
that do not satisfy certain registration requirements may seek the Minister's
permission to apply for registration on national interest grounds.[19]
4.16
Prospective EV manufacturer, Australian Clean Energy Electric Vehicle
Group (ACE-EV) suggested that this test was difficult to meet for start-up manufacturers.[20]
Ms Claire Johnson, Chief Executive Officer from Hydrogen Mobility Australia suggested
that the ATS should be reframed 'around zero- and ultra-low emission vehicles'.[21]
Ms Johnson continued:
When [the ATS] is set to cease with, at this point, no future
assistance available in the form of an automotive scheme, we think that can
send a strong signal to international companies who are looking to invest in
Australia.[22]
4.17
Hyundai's submission said that funding is available for research and
development (R&D) under the ATS and that this should be further prioritised.[23]
Tritium suggested that the ATS be extended to component manufacturing, noting
that 'grant programs are vital in supporting entrepreneurs who may be building
or seeking to build a business in the EV industry'.[24]
Assembly of imported parts
4.18
Some submitters and witnesses have expressed their support for EV manufacturing
based on the local assembly of imported pre-built parts. Volvo confirmed that it
is currently contemplating such an approach in relation to buses:
Volvo Bus also sees a future where we will be able to provide
local manufacturers in Australia with a chassis product that can be bodied
locally here in Australia. This will allow the same high standards of body
building to deliver safe, reliable and [Australian Design Rules] compliant
vehicles manufactured here in Australia, sustaining a vibrant and specialised
body manufacturing industry.[25]
4.19
In its submission, Uniti Australia said that it 'is designing a vehicle
to be assembled in Australia by Australians and for Australians' from imported
parts.[26]
Dr Michael Molitor, Chairman of Uniti Sweden AB (parent company of Uniti
Australia) explained that his company expected to be manufacturing 'up to
100 000 units within three to five years' in Australia.[27]
Mr Greg McGarvie, Managing Director of the ACE-EV provided details about his
company's two-stage approach for its Australian EV manufacturing plant:
We're taking a low-risk approach. Initially we were looking
at $5 million to get the assembly plant. We've got an assembly facility
available to get that set up and get their components in CKD and then, as soon
as it looked like there was interest and appetite for more vehicles, to the
second stage, which is full manufacturing here. In other words, we'd be doing
carbon fibre structures here, their panels here, supply chain—we've been
contacted by various lithium suppliers. We've got quite a few different supply
chains wanting to link in with us. We've got research facilities wanting to
link in with us. As you know, the carbon fibre research in Australia is quite
advanced.[28]
Retrofitting electric drive trains
4.20
As part of this inquiry, the Committee visited the SEA Electric
manufacturing facility in Dandenong, Victoria (see Appendix 3). SEA Electric is
an Australian-based company that initially retrofitted electric powertrains and
batteries to a wide range of commercial buses and trucks. SEA Electric now
supports the importation of gliders—a manufactured vehicle without a
powertrain—to which SEA Electric fits a powertrain and batteries providing a
fully electric vehicle to their clients. The Group Managing Director of SEA
Electric, Mr Tony Fairweather, described a future scenario where local
manufacturing may form part of the light truck manufacturing process:
The chief engineer from Isuzu Australia visited yesterday. He
explained how the pilot process at the moment in their particular case involves
substantial testing and evaluation of half a dozen vehicles, which are going
into service with some of Australia's largest operators of trucks later this
year. Their hope and intention is to potentially be producing their glider
vehicles, assembled in Australia with our driveline technology in them, early
next year or sometime next year. At the moment, everything they do right now,
which is up to 10,000 units a year, is 100 per cent imported internal
combustion engine product. Isuzu is an example of a company that is very
progressive and working towards an electrification option with, hopefully, some
local content. That opportunity for others is there. Our intention is in
licensing our technology but also very much in having a local assembly element
for our products and for end users. It's kind of a hybrid approach.[29]
4.21
Mr Fairweather noted that it was not only the new segment of the truck
market that is looking to convert to fully-electric, there are also those who
may seek to retrofit existing trucks with end of life conventional powertrains.[30]
Mr Fairweather asserted that SEA's all-electric commercial trucks now 'had
payback periods of three or four years based on the total-cost-of-ownership
model'.[31]
4.22
In October 2018, the Victorian Government announced it had signed an
agreement that would result in SEA Electric establishing an additional factory
in the regional town of Morwell in Victoria's Latrobe Valley. Mr Fairweather
estimated that the Morwell plant could build 2 400 four-tonne vans and commuter
buses, and employ up to 500 workers over the next five years. The plant is
expected to be up and running in less than a year and generate about $200
million in economic activity.[32]
4.23
The Australian Productivity Council put forward its views on a more
cost-competitive manufacturing approach that would be better suited to a lower
volume producer such as Australia:
The business concept had three main features.
Firstly, it proposed a way of building cars on a common
flexible platform (CFP) to substantially reduce initial development and tooling
cost per model at the expense of a higher base unit cost. Trading up-front
costs against unit costs in this way would provide better production economies,
more variety and shorter model cycle times at all volumes below 40,000 annual
units than the conventional manufacturing methods.
Secondly, the business proposed a different plant format,
similar to production concepts developed by Volvo at Uddevalla in Sweden, as an
alternative to the Toyota Production System (TPS). The proposed plant design
had fixed assembly stations as distinct from a moving assembly line with part
sets delivered sequentially to the workspace for assembly by a skilled
two-person team completing one vehicle per shift. Such a plant is much less
expensive to build, is more flexible, offers higher worker morale and a
flatter, less expensive, management structure than a conventional plant.
Thirdly, the business proposed a direct-selling model from a
digital platform supported by company-owned sites in shopping centres, a model
subsequently demonstrated by Tesla in Australia. This would collapse the dealer
margin into the producing business and enable solid profit margins, budgeted at
30%, providing rapid growth through retained earnings while offering customers
an ultra high quality product at a reasonable price.[33]
4.24
Mr Reynolds described how Precision Buses has used existing local
Australian engineering and design capability, previously harnessed for car
manufacturing to reimagine how buses are built. Instead of importing chassis
and fitting a coach body and other fittings as has been done in the past,
Precision Buses is looking at how it can bring together bus components from a
range of local and imported suppliers to build a product that meets their
client's requirements:
We've manufactured two electric buses to date that are being
prepared to go into trial. The aim of those buses is to look at how electric
drive line is affected by mass transport patronage, topography, traffic
structure in terms of time and delay, and also weather conditions. We also
manufacture an architecture which [has] moved away from the traditional chassis
and coach into an integrated model which allows us to become an [Original
Equipment Manufacturer (OEM)] in the bus manufacturing space. This allows us to
integrate various technologies from partners, whether that be drive line from
other OEMs or autonomous technologies from other companies, which allows us to
try and connect mass transport artery with last mile solution so that we have
an integrated solution. By setting that up in a local condition, we're able to
bring economic benefit to suppliers and manufacturers locally. We use the
existing capability that was available with OEM manufacturers in the passenger
car space to engineer for us today.[34]
4.25
One of the benefits to manufacturing locally are the synergies that could
be generated by having collaborators co-located, particularly in regard to
emerging technologies such as automation. Two companies, EasyMile and Transit Australia
Group, have announced plans to manufacture autonomous vehicles in South
Australia.[35]
Mr Simon Pearce, Head of EasyMile Asia-Pacific described EasyMile's
relationship with Precision Buses as 'seamless' when integrating their
technology. Mr Pearce suggested that automated vehicles are a parallel
technology that would develop side by side with electric and that it made sense
to co-locate where synergies might be gained for both parties.[36]
EV component manufacturing
4.26
The Committee heard that 'Australia has the skills needed to manufacture
EVs and components like battery cells, motors and power electronics'.[37]
The MTAQ noted that 'Australia has always been an effective supplier of
components'.[38]
4.27
Monash University submitted that Australia would need to be 'selective'
in deciding where to focus in regards to manufacturing EVs or components. The
submission suggested that:
Areas of strength lie in development of [Intellectual
Property], protection and nurturing of emerging energy storage technologies and
integrated systems for electric vehicles developed in our innovation system so
that we are better prepared for the next-generation of technologies required
for the EV market.[39]
4.28
Associate Professor Nesimi Ertugrul from the School of Electrical and
Electronic Engineering at the University of Adelaide put forward a similar
view:
My view is: why don't we focus on some value-added part of
these electronics—from the battery level, motor control level, similar
topology, similar developers. If this continues happening, we can become an
electronic nation. We can compete, with electronics all produced in automated
manner without touching a single hand. That's how I see it.[40]
4.29
During the inquiry, the Committee visited the Nissan Casting Plant
Australia (NCAP) in Dandenong, Victoria (see Appendix 3). The plant casts,
machines and assembles components for motor vehicles in the Nissan range with
parts exported to Japan, Thailand, Mexico and the United States. The plant
employs nearly 150 people and operates six days per week.[41]
NCAP's submission stated:
NCAP produces six key components for Nissan EV and hybrid
vehicles that are sold globally. The growth of EVs globally is allowing us to
not only expand our workforce, but also develop talents in areas such as
engineering, manufacturing, logistics and more.[42]
4.30
Pilbara Metals Group (PMG) commented that Australia's large reserves of
raw materials required for battery manufacturing 'has allowed companies to
[proceed] with planning and engineering studies to produce various components
of batteries in Australia'. PMG suggested that production of battery cathodes
could be a logical starting point.[43]
4.31
MTAQ submitted that the manufacture of a key component such as a battery
pack in Australia could lead to other parts of the EV manufacturing chain also
being based in Australia:
The economics of vehicle manufacture tends to indicate the
most important component is the battery pack. The geographic sourcing of these
items can be expected in large part to determine the architecture of the future
electric vehicle manufacturing. Tesla has demonstrated the economic power that
battery manufacturing confers on an OEM electric vehicle producer.[44]
4.32
The Committee has also heard that Australia has significant,
high-quality deposits of rare earth elements (REE) that are used to manufacture
permanent magnets for EVs and 'for electric generators that power wind
turbines'.[45]
China currently dominates the mining of REE and the manufacture of permanent
magnets. Deakin University argued that there is an opportunity for Australia to
take advantage of its reserves, to build local manufacture of value-added
products and to do so in an environmentally responsible way.[46]
The University of Adelaide submitted a similar proposition:
Australia can also develop high quality brushless permanent
magnet motor manufacturing facilities used in EVs which rely on two critical
value added materials: copper and rare earth magnets.[47]
Research and development
4.33
Many witnesses and submitters highlighted the key role that R&D has,
and could, continue to play in underpinning Australia's future automotive
manufacturing capacity. This R&D runs the spectrum from academia through to
in-house OEM R&D centres.
4.34
The Committee has heard that Australia is an R&D hub for major OEMs
such as Ford, GM Holden and Toyota in the Asia-Pacific:
Currently, Ford has a design/styling, engineering and
homologation/testing team in Australia, and General Motors and Toyota have
their design/styling and small engineering teams in Australia.[48]
4.35
Mr David Magill, Director, Government Relations and Public Policy, GM
Holden explained that GM Holden 'are now doing over $120 million worth of
R&D annually in Australia each year and our engineering program in advanced
vehicle development is going to be working on electrification projects for GM'.[49]
The Committee also heard that GM Holden is expanding this capacity in advanced
vehicle development—the 'area between pure research and development and
establishing programs that are technically feasible and business case feasible
and can be produced'.[50]
4.36
In its submission, Hyundai noted that it invests in Australian R&D
and the value of this work:
This is valuable, highly skilled work that both secures and
develops automotive engineering expertise in Australia and should continue to
be supported through a dedicated program if the country is to recognise the
sector as having strategic importance to the economy.[51]
4.37
Noting the importance of batteries not just in motor vehicles, but also
for stationary energy storage, the CSIRO is contemplating establishing a new
future science platform focusing on the lithium value-chain. This would place
it as one of the CSIRO's six priority areas for future scientific research.[52]
The CSIRO has also reiterated to the Committee the importance of its
partnerships with industry as a means to commercialise research outcomes with
benefits for both industry and CSIRO.[53]
4.38
Associate Professor Patrick Howlett from Deakin University told the Committee
that research in the automotive sector is constantly evolving as a result of
changing priorities and scientific breakthroughs. Associate Professor Howlett
raised the example of advances in lithium metal electrodes in high-energy
batteries:
The [United States Department of Defence] made a directive to
essentially investigate the lithium-metal electrode for high-energy batteries
for electric vehicles, and they have the target of 500 watt-hours per kilo.
There were a lot of slogans that went around that. What that has driven is
research in the US on the lithium metal electrode, and then that has further
driven worldwide research to the point where now there have been rapid advances
in that technology. Where not so long ago that was essentially ignored as a
potential technology, now it's probably the most likely next technology. That's
the metal electrode; that's only the bottom half of the battery, if you like.
The cathode remains a problem, and there are a range of technologies that can
be addressed there.[54]
4.39
In its submission, Deakin University flagged a number of constraints to
research in the automotive sector. The most significant of these is the lack of
students available to undertake post-graduate study and the difficulty in
recruiting automotive engineering researchers. This difficulty stems from the
perceived lack of employment opportunities in the automotive sector and complications
accessing student visas.[55]
During the Adelaide hearing, Professor Rocco Zito, Head of Civil Engineering,
College of Science and Engineering at Flinders University noted the current
professional development and employment pathways that exist, but flagged that more
could be done to ensure that employment opportunities exist for these students
at the conclusion of their studies:
I think there is a need to bring some coherence to this
debate in the form of an industry roadmap for EV and AV in Australia to provide
short- and medium-term guidance to how we can maximise our participation in the
value chain in both inputs like batteries and taking on that larger challenge
and opportunity of being part of a global EV-AV industry into the future. We
should never rule that out in the great sweep of history. Even in the wake of
the closure of the auto industry, which hurt us in South Australia so badly,
there are plenty of skills and capabilities available to be redeployed cleverly
in a very high value industry at its best, EV and AV.[56]
Industry 4.0
4.40
A key opportunity for the manufacturing of EVs and associated
componentry in Australia is the worldwide phenomenon of 'Industry 4.0'. This
refers to what is being termed as the fourth industrial revolution—that is,
technological developments such as the improvement of artificial intelligence
and machine-to-machine integration across 'almost every industry worldwide'.[57]
In a recent article, Dr Jens Goennemann, Managing Director, Advanced
Manufacturing Growth Centre described the benefits of Industry 4.0:
Industry 4.0 can start with as little as sticking a sensor on
a piece of equipment so that one can monitor where it is or what it does. In
the longer perspective though, it is about establishing a relationship with
embedded intelligence across the entire manufacturing process from research and
design through to the final customer engagement. If we get this right, then customer
feedback loops back into the R&D process and starts the next iterative step
in delivering high-quality outcomes and rich customer experiences.[58]
4.41
Of most relevance to this Committee is the increase in manufacturing
automation. The Boston Consulting Group explained how increased automation will
also lead to significant decrease in battery price:
By transitioning to the factory of the future [Industry 4.0],
producers can reduce total battery cell costs per kilowatt-hour (kWh) of
capacity by up to 20%. The savings result from lower capex and utility costs
and higher yield rates. The production-related costs (excluding materials) can
be reduced by 20% to 35% in each of the major steps of battery cell production:
electrode production, cell assembly, and cell finishing. Electrode production
benefits from faster drying times that increase yield rates and reduce capex
for equipment. In cell assembly, data-driven automated adjustment of parameter
settings increases accuracy and reduces production times. Cell finishing is
enhanced by shorter times for formation and aging, which significantly reduces
capex requirements.[59]
4.42
Professor Peter Newman highlighted the opportunities that Western
Australia has in taking advantage of Industry 4.0 developments:
Fourth stage technologies offer WA the opportunity to develop
a much larger industrial base that is complementary to its world-leading
resource extraction sector. These technologies shift the competitive advantage
of early stage value adding away from low cost labour countries to the earliest
point in the value chain where all the input materials can be brought together
for highly automated manufacturing processes. Components are then shipped to
the major global manufacturing centres for later stage manufacturing where proximity
to markets or low-cost labour still afford an advantage. WA is in the unique
position of having abundant quantities of almost all the New Energy metals,
giving it a large advantage in electro-chemical processing.[60]
4.43
Automated manufacturing will have a lower labour requirement and allow
Australian firms to compete globally. Deakin University's submission indicated
the need for Australia to adopt and develop Industry 4.0 frameworks and
technologies to be competitive in EV manufacturing:
The competitive manufacture of electric vehicles in Australia
will need to leverage Australia's research and development capabilities to
deliver future integrated factories. These Industry 4.0 facilities will operate
as a 'system of systems' through intelligent machines, human factor
integration, and integrated supply chains.[61]
4.44
Deakin University also anticipated the benefits that would eventuate
from adopting Industry 4.0 framework in electric vehicle manufacturing through
the ability to 'participate in the global supply chain' without having to
commit to a full-scale 'end-to-end vehicle manufacturing industry'.[62]
4.45
The concept of Industry 4.0 was discussed in a November 2015 report of
the intergovernmental Australia-Germany Advisory Group, Collaboration,
Innovation and Opportunity.[63]
Recommendation 10 of this report called for 'initiating a collaborative
approach to the development of global Industry 4.0 standards'.[64]
4.46
The report of the Australia-Germany Advisory Group resulted in the
creation of the Prime Minister's Industry 4.0 Taskforce (now the Industry 4.0
Advanced Manufacturing Forum).[65]
The Taskforce and its successor have fostered an industry relationship with the
German Plattform Industrie 4.0, and supported Industry 4.0 test laboratories in
Australian universities.[66]
Battery manufacturing and commodity value-adding
4.47
Earlier in the report, the Committee discussed the benefits for the
mining sector from an increased use of EVs both here and in Australia.[67]
The future of EV manufacturing will lead to an increase in demand for a number
of key resources including copper, nickel, cobalt and lithium. Given the
anticipated increase in demand for EV manufacturing in the coming decades,
there could be a significant upsurge in the value of these minerals.[68]
The Electrical Trades Union highlighted Australia's natural advantages:
Australia has some of the highest grade, and largest,
deposits of Lithium and Vanadium in the world, particularly in Western
Australia. Western Australia is also currently the largest producer of lithium,
which is necessary to supply batteries for the emerging EV market.[69]
4.48
Bloomberg NEF projected that 'global demand for metals and materials
used to produce lithium ion batteries will increase 25-fold by 2030'.[70]
Dr Howard Lovatt, Team Leader, Electrical Machines at the CSIRO made the point
that Australia's diversity of mineral resources makes it well placed to take
advantage of any changes to battery chemistry and composition:
Generally in terms of batteries it most definitely is an area
that's changing rapidly, and new developments are occurring, and that will mean
that some minerals that were important suddenly become not important and vice
versa. Particularly when you get a big growth in an industry like lithium
batteries, it does put stress on the supply of some minerals, so then
everyone's motivated to change the composition of the batteries to avoid those
minerals. So this is very much a moving target. But I guess the good news for
Australia is that we're well supplied with lots of different minerals, so it's
likely to benefit Australia regardless of the final commercial outcome.[71]
Commodity value-add
4.49
Mr Warren Pearce, Chief Executive Officer of the Association of Mining
and Exploration Companies explained the lithium value chain from mining to
battery manufacture:
we've broken the value chain into the five steps toward the
creation of manufacturing of batteries: the first step being mining
concentrate; the second step being refining and processing; the third step
being electrochemical processing; the fourth step being the production of
battery cells; and the final step being the assembly of batteries.[72]
4.50
Mr Pearce noted that Australia currently only participated in the first
step—mining the raw materials—but that involvement in the subsequent stages could
bring huge economic returns to Australia saying that many Australian companies
'are now quite legitimately looking to process or value-add their materials to
see if they can get into a greater part of the value chain.[73]
4.51
Currently, it is estimated that Australian mining companies capture less
than 0.5 per cent of the lithium chain.[74]
Deakin University agreed with this estimation stating that 'there is a great
opportunity for Australia to capture a larger part of the value chain of
lithium ion batteries, by not only exporting the lithium minerals, but also by
designing and manufacturing batteries'.[75]
4.52
Mr Pearce provided the Committee with examples of a number of Western
Australian mining and exploration companies where Australian mining and
exploration companies have partnered with larger international companies with
capital and expertise in processing in order to build processing facilities for
lithium and other commodities.[76]
4.53
Mr Pearce discussed the need for linkages to be facilitated between
Australian mining and exploration companies with international processing
companies in order to import much needed expertise and capital. This expertise
would enable Australian businesses to value-add our mineral resources on-shore
for export or domestic use:
In order to achieve that, there are some barriers that our
report has tried to identify, primarily being that our member companies are
mid-tier or small-cap mining companies. They don't have large balance sheets
and they require support to find investment to build these types of facilities.
Also, in order to move into that space, we're capable explorers and miners but
we are not processers or refiners. We need to access the proprietary knowledge
and technical expertise to undertake that successfully. To make that
possibility a reality, our organisation has been promoting the opportunity for
partnerships between international companies that hold this knowledge and
Australian mining companies.[77]
4.54
The 2018 report titled Lithium Valley: Establishing the Case for
Energy Metals and Battery Manufacturing in Western Australia observed how
trends such as automation are changing the economic paradigm of value-adding
raw minerals:
Historically, it was more cost effective to value add closer
to large markets or in countries with large, low cost workforces. This is no
longer the case. Information technologies, artificial intelligence, automation
and new energy systems now favour manufacturing at the earliest point in the
value chain where all the input materials can be brought together in a low, cost
effective way.[78]
4.55
This same report quantified the projected economic importance of
value-adding. An integrated approach that focused on mining, refining with 10
per cent electro-processing (the first three steps that Mr Pearce outlined) is
projected to result in over 100 000 jobs, economic investment of over $34
billion and an economic contribution of $56 billion per annum by 2025. This
compares to a mining only scenario whereby less than 30 000 jobs are
created and total investment of nearly $14 billion.[79]
Battery manufacturing
4.56
In addition to processing and advanced refining of minerals, there is an
opportunity for Australian companies to value-add refined minerals into battery
cells and then assemble into batteries. The University of Adelaide stated that
Australia could play a part in the 'automated production of batteries and
battery management systems in [the] EV supply chain'.[80]
4.57
Mr Brian Craighead, Director of Renaissance Energy told the Committee
about his company's intention to construct a lithium-ion battery factory in the
Northern Territory. [81]
Mr Craighead explained the benefits to his company of building tailored
products in Australia:
We are manufacturing a particular type of battery cell that
works better in hot climates. That's South-East Asia and Australia. Part of the
reason we're up in Darwin is that the export capability is very good for us
when it comes to South-East Asian markets. Ours is, we think, about 70 per cent
an export business, but Australia is an important market for us in both the grid
market and the electronic vehicle market. We've met a few folks who seem to be
quite ambitious with plans for electronic vehicle manufacturing. An EV,
fundamentally, is a battery on wheels. So for us it's a very attractive market.
We can customise batteries and stick them in EVs. For hot-climate [EVs], we
think that there will be a very clear market.[82]
4.58
Mr Craighead also noted that the capital expense of building an
automated factory is 'not what it once used to be', and explained the
counterintuitive proposition that Australia could find itself as a leader in
extracting the raw materials required in batteries and manufacturing the
batteries themselves but not having the capacity in Australia to process and
refine the raw material to battery manufacturing grade:
The great sadness of Australia—the kind of twist here—is
that, although we have all the raw materials we need to manufacture
competitively lithium-ion batteries in Australia, the reality is that all those
raw materials without exception are mined and shipped overseas to be processed
to battery grade and then reimported; we have to re-import. Most of the margin
is given overseas because there aren't processing facilities locally for
battery-grade raw material.[83]
4.59
Mr Craighead was confident that the establishment of a battery
manufacturing sector in Australia could provide the critical mass to encourage
local miners to develop processing and refining capabilities:
What they need is security in offtake. If there is enough
confidence in forward orders, people can justify and bank the capital
investment to do the processing locally. In some cases—lithium, less so—it's
quite expensive to bring a processing facility on shore. And it's the process
as well, because some of them are power hungry and with some of them you have
to be very careful that you're not hurting the environment. So because of the
cost involved all of them need security in forward orders. Basically, they need
to know if they have enough orders for the next three years to justify the capital
investment.
And here's how you get that: we will bring some level of
security in forward orders to these folks locally, because, obviously, the
reason you exist is to buy Australian. But if another factory comes up—if the
Townsville comes up—it will be much bigger than ours; it's a very differently
sized facility. If that goes up it would bring even more security in forward
orders. So, really, it's just like any bankable project: the more forward
orders you've got then the more comfortable the lenders are and the more
comfortable the investors are. That's what will suit our local processing. For
every dollar of benefit and economic benefit that our little factory brings
there's about six that go to the raw material producers so that they can get
processing. There's much more in it for Australia if we can have them
processing to battery grade, rather than our little factory.[84]
4.60
Two battery manufacturers, Sonnen and Aplha ESS, have recently announced
that they will manufacture lithium-ion home batteries in Adelaide.[85]
4.61
Professor Mainak Majumder of Monash University was more cautious in his
advice to the Committee:
My view is that because battery manufacturing is so well
established in South-East Asia and in Japan and that they're so good at that we
might not be able to compete with them in battery manufacturing. But we could
possibly think about the resources that go into battery manufacturing, and that
could be a much better approach for us to invest in.[86]
4.62
Mr Pearce observed that the establishment of a local battery
manufacturing sector would be beneficial for mining and processing companies
'as a local market to sell their product into'.[87]
An Australian-based battery manufacturing sector would also have flow-on benefits
to other industries 'such as the manufacture of new submarines in South
Australia which is expected to involve battery technology'.[88]
Battery technology and developments
4.63
At its Melbourne hearing, the Committee heard from a panel of academics
specialising in battery chemistry research who spoke about their research areas
and the implications this work would have on battery use into the future.
Associate Professor Patrick Howlett from Deakin University stated that his
focus was on 'next generation prototype batteries with new materials that have
superior properties, for example, lighter weight'.[89]
Associate Professor Howlett also described the industry's move to lithium-ion
batteries with higher levels of cobalt:
The main attractiveness there is their higher theoretical
energy density or specific capacity, which is the amount of charge they can
store per gram, as well as their higher voltage.[90]
4.64
Mr Ali Asghar, Senior Associate for Power, Energy Storage and EVs at
Bloomberg New Energy Finance explained that as demand for particular minerals
increases with battery demand, this will drive innovation and amongst the
battery industry to modify the chemical composition of batteries to reduce
battery input costs:
We do look at battery chemistry changes in the chemical composition
of batteries—the amount of cobalt, lithium, nickel, manganese composition
within batteries. We do expect a change towards chemistries with a lower
composition of cobalt, mainly because that is a metal that we expect to be a
bottleneck in lithium-ion battery manufacturing. It is basically a road block
in putting pressure down on lithium-ion battery pricing.[91]
4.65
Associate Professor Howlett noted that higher energy density can pose
difficulties from an operating perspective as they are restricted in how
quickly the batteries can be charged.[92]
4.66
Professor Baohua Jia, Research Leader at the Swinburne University of
Technology highlighted her team's work on supercapacitors, which are 'a very
good alternative for the current batteries in terms of safety issues, lifetime,
cost and also environmental concerns'.[93]
4.67
The University of Adelaide has projected that by 2030 'silicon carbide
and gallium nitride based switching devices will drastically change the power
electronics systems used in EVs (including battery chargers and motor drives)'.
The use of such devices will 'improve efficiency, operating temperature,
reliability while significantly reducing system size and weight'.[94]
4.68
Nonetheless, many witnesses argued that despite these advances lithium-based
batteries would remain the dominant underlying chemistry in batteries well into
the future.[95]
Mr Asghar affirmed this view:
Absolutely, lithium-ion batteries have an incumbency
advantage. They have governments that are supporting the technology,
governments that are supporting the manufacturing—for the electric vehicle
industry and lithium-ion battery manufacturing. That gives me a little bit of
confidence that, at least in the next five to seven years, lithium-ion
batteries will likely be the major source for electric vehicles.[96]
4.69
Associate Professor Howlett added to this noting that 'there are a
number of fundamental barriers to making [lithium-ion batteries] work well,
particularly when we try to achieve long cycle lives or the high rates that we
need for acceleration'.[97]
4.70
Importantly, this dominance of lithium-ion is likely to underpin the
continued fall in battery pricing and, in turn, the improved affordability of
EVs. The Committee heard that the average pricing of lithium-ion battery pack
is expected to fall from its current pricing of $209/kilowatt (kW) to $70/kW by
2030.[98]
Mr Asghar explained the reasons for this projected trend:
It's a story of mass manufacturing—so economies of
scale—technology development and a major push towards electric vehicles.
Electric vehicles are currently the biggest consumer of lithium-ion batteries.
They've surpassed consumer electronics or stationary storage. Because of that
demand for lithium-ion batteries there's been a lot of R&D into the
technology and there's been a lot of investment into manufacturing capacity,
specifically in Asia—in China, South Korea and Japan. Economies of scale have a
big role in this. We've seen this in solar panels, where the Chinese started
entering the solar PV manufacturing sector and brought the cost down
considerably over the last decade. It's a similar trend that we see in
lithium-ion batteries. I would say: technology improvement and economies of
scale.[99]
Figure 4.1:
Lithium-ion battery prices, historical and forecast[100]
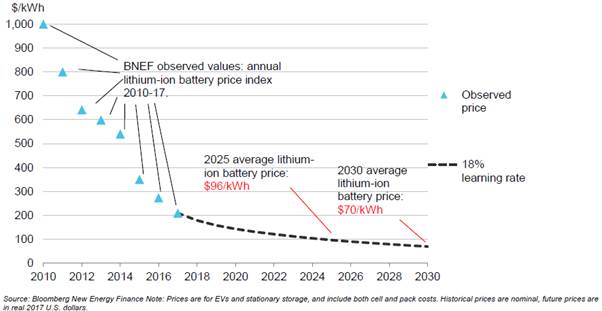
4.71
Mr Fairweather also noted:
With the technology developing and density increasing in
batteries at the scale and rate that they currently are, in the very short
term—maybe 12 months to two years—the battery sizes will start to be reduced
with range still being retained.[101]
4.72
The International Energy Agency's (IEA) Global EV Outlook 2017,
noted that '[r]esearch, development and deployment...and mass production
prospects are leading to rapid battery cost declines and increases in energy
density'.[102]
Figure 4.2 is taken from the IEA's report and shows the evolution of battery
energy density and cost.
Figure 4.2:
Evolution of battery energy density and cost[103]
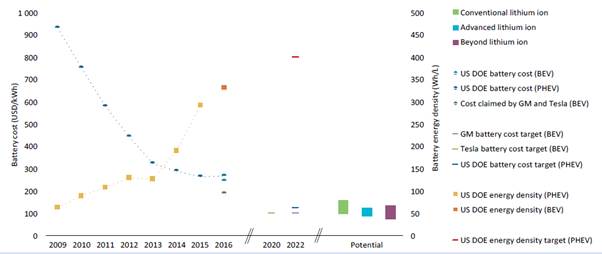
Battery recycling and repurposing
4.73
As the number of EVs rises and the batteries reach end-of-life, a number
of witnesses have identified the recycling and repurposing of EV lithium-ion
batteries as both a significant challenge and opportunity. The Queensland
Department of Transport and Main Roads (DTMR) claimed that significant prospects
exist for Australian businesses in relation to battery recycling:
As a greater number of EVs are brought into the vehicle
fleet, there will be opportunities to create industries around recycling and
reusing EV batteries. EV batteries can be used for stationary storage, and
following this, the raw materials can be recycled to create new batteries.[104]
4.74
According to the CSIRO only about three per cent of lithium batteries
currently sold in Australia 'are being captured and sent for recycling
off-shore'.[105]
In its submission, MTAQ referred to a CSIRO report projecting between
100 000 and 188 000 tonnes of lithium battery waste by 2036, noting
that 95 per cent of this waste could be recycled into 'new batteries or used in
other industries' and yield an economic benefit of between $813 million and $3
billion by 2036.[106]
4.75
However, Dr David Harris, Research Director for Low Emissions
Technologies and Energy at the CSIRO acknowledged that there are serious
challenges in the recycling space, but that these are not insurmountable:
We have projects underway now looking at how we can help
companies who currently recycle some components of batteries adapt their
processes to accommodate the changing composition of batteries, the higher
metal contents, the different metals that are coming on—so, how we fit into
existing processes and add new capability as the batteries change. We're
helping to do that. In some cases the materials get recycled either back to the
manufacturer or for different purposes altogether in Australia. We're now working
with groups looking at different applications and separating those safely,
because just recycling them itself is not a trivial process; that's a process
that requires safety procedures. Batteries still have some charge and can still
catch fire in those processes. We are doing work with people to try to develop
efficient processes for battery recycling.[107]
4.76
Some manufacturers such as Tesla and Toyota are already taking
responsibility for 'whole of the battery life'.[108]
Toyota has established a hybrid EV Battery Recycling Program with cash rebates
and discounts for the return of EV batteries.[109]
Whilst a recent media article claimed that 60 per cent of Tesla batteries are
recycled with a further 10 per cent being reused in some form. Tesla is working
towards a closed manufacturing loop that 'reuses the same recycled materials'.[110]
4.77
Dr Dale of the MTAQtold the Committee that there were many businesses excited
by the commercial opportunities presented by battery recycling and ready to
take up the challenge. Notwithstanding this confidence, many of these
businesses need support to understand some of the technological issues
associated with this industry. Dr Dale stated:
If we can develop the technology to support businesses with
that interest then that's where Australia will win in the longer term.[111]
4.78
In this context, the Committee notes the recent grants from ARENA and
the CEFC to Melbourne-based company Reelectrify who are seeking to
commercialise battery recycling technology.[112]
4.79
Dr Matthew Stocks, Research Fellow at the College of Engineering and
Computer Science at the Australian National University provided a practical example
of how a used EV battery might be repurposed:
Electric vehicle range is important. Electric vehicles have a
more limited battery life than stationary energy. As battery capacity
decreases, you are likely to say: 'I don't want this battery anymore; I want a
new one.' That battery still has a significant life potentially for other
applications like replacing a Tesla Powerwall in stationary energy, where I
don't actually care if I put in another three batteries—instead of putting in
10, I put in 13—because there is no real space cost. So I suspect that a lot
will go into re-use rather than recycling, to begin with.[113]
4.80
Dr Howard Lovatt, Team Leader, Electrical Machines, CSIRO noted that
recycling car batteries may in fact be a more straightforward process than
recycling batteries associated with smaller, personal devices:
To make one observation on that, with a vehicle it is a lot
easier to capture the battery at the end of life because there is already
significant infrastructure for recycling the vehicle as a whole and the
batteries could be an add-on to that, whereas, like your phone or your laptop
batteries, it is much harder to actually capture the battery at the end of
life.[114]
Manufacturing and installation of charging infrastructure
4.81
The lack of charging infrastructure is a barrier to increased uptake of
EVs. The Royal Automobile Club of Victoria (RACV) cited a recent survey that
found 80 per cent of 'respondents consider the availability of public fast
charging (ie. 15 minutes to full charge) to be an important factor in
influencing their decision to buy/own an electric vehicle'.[115]
Furthermore, over half of respondents to the survey 'believe government should
implement subsidies to reduce the cost of installing home charging, and provide
public charging infrastructure'.[116]
4.82
Although Australia currently has a relatively high ratio of public
chargers to EVs—about one charger to every six EVs—the low number of EVs and
the large geographical area of Australia mean that this number will need to
continue to grow to maintain this ratio and public confidence in using EVs
across the country.
4.83
In its submission, the Australian Logistics Council (ALC) described the
three types of charging infrastructure—'home charging, public charging and
rapid/fast charging' and noted that :
Home charging and public charging can further be grouped as destination charging – a slow charge
designed to help motorists travel in metropolitan centres.
Rapid/fast charging is analogous to highway petrol stations
and is known as journey
charging. As its name implies, it is designed to rapidly charge an
electric vehicle for longer journeys.[117]
4.84
There are currently considerable opportunities for local companies to
take advantage of the forecast increased demand for manufacture and
installation of charging infrastructure for residential, commercial and
government applications.
Home charging
4.85
The vast majority of EV charging is expected to occur at home, with
about 70 per cent of EVs having a dedicated charging unit either at home
or work.[118]
Home charging at its simplest is connecting the EV to a regular household power
outlet which provides the equivalent of 100 kilometres of charge in 17 hours.
This can be upgraded to a basic AC charger known as a "slow" or
"trickle" charger which can fully charge a vehicle overnight.[119]
4.86
About 85 per cent of kilometres travelled in Australian passenger cars
are classified as short range driving, that is generally less than 100 kilometres
from home.[120]
Another survey showed that 'more than 99% of daily trips were under 50
kilometres, implying a round trip of 100 kilometres.[121]
Most of this driving is commuting to work, study and recreation; visiting
friends; and shopping. With newer EV models having a range of over 350 kilometres,[122]
a home charger will meet the average day-to-day needs of most Australians. The
Tesla Owners Club of Australia (TOC) confirmed this and made the point that
most owners will not require public charging the majority of the time.
The day to day requirement does not require high speed
charging, with vehicles typically sitting idle for ten or more hours overnight
or for a similar period during the day whilst the owner is at work.[123]
4.87
Even so, people for whom most charging is undertaken at home will still
have a public charging requirement for long-haul trips.[124]
4.88
TOC noted that the limitation to home charging, particularly those who
live in apartments is the availability of charging points:
The key is availability, particularly for those who live in
apartments. This can be addressed through building codes for new residential
and commercial properties. As long as the electricity supply to the premises is
appropriate the charging facilities do not need to be anything more complex
than a standard 15A or 3 phase outlet which can be used with a suitable lead or
adaptor.
This will not immediately address the demand in existing
buildings and it may be appropriate to make grants available to local councils
or other authorities to provide publicly accessible charging points on street,
in car parks and places of work.[125]
4.89
In its submission, the vehicle manufacturer Tesla confirmed the difficulties
for apartment owners and observed that another barrier to home charging is for
those who rent homes:
Customers who are keen to purchase electric vehicles in
Australia are often unable to do so if they live in apartments or are renting
their home. Some are able to install charging quickly. However, others can be
delayed because strata meetings for their building are very infrequent or have
no clear process to follow for charging installations. Customers can also be
faced with unreasonable demands or objections from landlords or strata Committees.[126]
4.90
An Energeia report also noted that EV 'drivers without access to home
charging must rely entirely on public charging'.[127]
The next section explores public charging stations.
Public charging stations
4.91
As noted earlier, 'two thirds of motorists indicate that a lack of
adequate charging infrastructure is the greatest barrier to purchasing an [EV]'.[128]
A small proportion of total Australian passenger vehicle kilometres are
classified as long-range driving—about 15 per cent. Public chargers are
primarily used for convenience but will also be used by drivers undertaking
long-range trips and for those who do not have access to a charger at home or
work. The Committee heard that public chargers form an 'important part of the
electric vehicle ecosystem'.[129]
4.92
During the inquiry, the Committee heard about some of the businesses
that are benefiting from the growing demand for public charging infrastructure.
Mr Nathan Dunlop, the New Markets and Sales Analyst at Tritium, a
Brisbane-based company, provided a background on his company:
we're almost 250 staff now at Tritium. Those staff are in
engineering, automotive and high-tech roles, working on exporting our product
overseas. I guess the thing to note here is that those jobs also create
downstream jobs throughout the supply chain. We create installation,
maintenance and field service opportunities for installers that are putting our
product in the ground. That's worldwide and in Australia. We also create jobs
in regard to the supply chain. As you saw, our product has very many components
in it, and 40 per cent of that procurement spending goes to Australian
businesses at the moment. So those jobs are coming to Tritium but are also
creating downstream job impacts.[130]
4.93
Chapter 2 of the report described the different types of public charging
infrastructure. Level 2 chargers (slow chargers) can charge an average car in
4–6 hours; whereas level 3 chargers (fast/ultra-fast chargers) can charge a car
in as little as 20 minutes (even less for ultra-fast chargers currently under
development).[131]
A recent Energeia report estimated that up to 30 per cent of EV drivers will
rely on public chargers for 100 per cent of their EV charging needs.[132]
Level 2 public chargers are primarily used 'for public destination-based
charging locations to attract drivers' such as supermarkets or shopping centres.[133]
Level 3 chargers are mainly used for long-distance charging where an EV needs
to quickly recharge in order to continue its journey.
Highway charging
4.94
In its submission, Fast Cities Australia estimated that the optimal
spacing for an ultra-fast charging network would be 150 kilometres, and that a
network of this type would cost a minimum of $100 million.[134]
Fast Cities Australia also stated that 'ultrafast highway charging networks are
capital-intensive but cannot attract conventional equity and debt in medium
term due to revenue uncertainty'.[135]
4.95
A number of state governments and other organisations are establishing,
or planning to establish, new public charging infrastructure. Mr Paul Fox,
Head, Corporate Development at Fast Cities Australia told the Committee of
their intention to complete a network of fast chargers along the major
federally funded highways:
My colleague tells me that he could knock out 42 sites very
quickly. It's really a matter of the timing of funding. But our intention is to
have the Melbourne to Brisbane completed by the end of next year, and then we
would roll out the remaining 42 sites in the following year and six months. So
it's about a two and a half year process in total. We could go faster; we have
to be careful about going faster, because we need to match it to the growth in
demand. We're already going ahead of ourselves; we don't want to go too far
ahead of ourselves.[136]
4.96
The DTMR described the Queensland Government's Electric Super Highway
(QESH), which stretches from Coolangatta to Cairns and Brisbane to Toowoomba.
DTMR explained:
Fast charging stations have been built in Cairns, Tully,
Townsville, Bowen, Mackay, Carmila, Marlborough, Rockhampton, Miriam Vale,
Childers, Maryborough, Cooroy, Brisbane, Coolangatta, Springfield, Gatton and
Toowoomba. An additional charging site will be built at the Helensvale
Queensland Rail carpark now that the Commonwealth Games have finished, once the
carpark upgrade is complete.
Each site is no more than 200km apart and was chosen
considering the driving range of EVs, local amenities, and the local energy
network capacity. Sites are located close to amenities, such as cafes, shopping
centres and restrooms, allowing drivers to take a break to stop, revive and
survive while they recharge their vehicle.[137]
4.97
DTMR stated that the large rollout of charging stations has resulted in
a reduction in the ratio of EVs to public chargers from 10.5 to 4.9. This is
despite a 70 per cent increase in the EV fleet over the last two years.[138]
Ms Sally Noonan, Chief Economist at DTMR stated that the Queensland
Government's reasons for building the QESH was not just about refuelling
vehicles but also encouraging people to spend time in various locations around
Queensland:
It's quite a different experience. The Queensland
government's Electric Super Highway is not about just filling up in 10 minutes
and then you're gone. It's actually trying to, in particular, look at that
range anxiety around tourists, for example. That is where we see there's a real
opportunity, where people are going to spend some time in the location where
their vehicle is charging. It's quite a different proposition to the petrol
station kind of scenario that I understand.[139]
4.98
The Royal Automobile Club of Western Australia (RACWA) also described
the RAC Super Highway, 'a network of 11 publicly accessible EV fast charging DC
stations located between Perth and Augusta' (520 kilometres) in south-west
Western Australia.[140]
The NRMA stated that it intends to build 'Australia's largest charging [EV]
fast charging network' in NSW at a cost of $10 million.[141]
4.99
Mr Tim Washington, Chief Executive Officer at Jetcharge, a
Melbourne-based business explained how his business is benefitting:
JET Charge is what I would call a small business, one of the
beneficiaries of the downstream jobs that Tritium are talking about. We started
about five years ago, and we're now the leading installer of electric vehicle
charging stations in Australia, being the recommended installer for nine
vehicle brands nationwide. If you think of us as, basically, the people on the
ground actually making sure the infrastructure gets installed, we're those
people. We're the largest hardware distributor of charging stations in the
Australian market. We've seen a large growth period over the last two years in
the market. We currently employ 14 people in the head office and have a large
contractor network of electricians who perform installations for us. That comes
from a base of only two to three people, two years ago, and so we've seen some
good growth in the market. From my perspective, it's really important that
small businesses like ours have the room to grow into this new industry.[142]
4.100
Mr Washington also described an associated business called Chargefox:
Chargefox is basically a software business that controls the
charging stations. You need software to control the charging stations, and
Chargefox was born out of a joint venture between us and a software business.
It is another example of the new age of automotive, in terms of the
technologies that are required, and is another Australian-born business, which
currently employs four people.[143]
Metropolitan charging
4.101
A number of local governments have also declared their interest in
establishing public charging infrastructure within their local areas.[144]
4.102
The Committee heard that the ACT Government is funding '50 new EV public
charging stations in Canberra' at a cost of about $450 000.[145]
That works out to be $9 500 per charger.
4.103
Ms Michelle English, Associate Director at the City of Adelaide spoke
about the how the City of Adelaide was seeking to leverage private sector
capital to build charging infrastructure:
At a local level, we have several initiatives that
demonstrate our commitment and our leadership. In the last 12 months we have
co-funded with the state government, Esso power networks and Mitsubishi Motors
the installation of 30 off-street electric vehicle charging stations in our
council owned UPark stations and an additional 10 on-street electric vehicle
charging stations. We've also partnered with Tesla and our eight-bay electric
vehicle charging hub in Franklin Street to enable them to install four
120-kilowatt superchargers. We offer two hours free parking in selected high-profile
locations, such as the Franklin Street EV charging hub.[146]
4.104
Ms English continued describing incentives for local businesses and
community members:
In addition to infrastructure, our Sustainability Incentives
Scheme provides financial rebates to our businesses, property owners and
community for rebates of up to $1,000 for each fast charger less than 20
kilowatts, $5,000 for each superfast charger over 20 kilowatts, and $250 for
each electric bike charging station installed in the city.[147]
4.105
In its submission to the Committee, Jolt explained that it is building a
network of public chargers, 'providing free charging for users and free
installation for cities, funded by the billion dollar digital out-of-home
advertising market'.[148]
4.106
The UK Government, in its Road to Zero Strategy, noted that in addition
to charging at home overnight, charging at workplaces during the day will be
one of the 'most attractive options' as 'EVs go mainstream'.[149]
The UK Government has made funding available to private businesses and public
bodies through a Workplace Charging Scheme and recently announced an increase
in the levels of the scheme to provide up to £500
off installation costs of charging sockets deployed at workplaces.[150]
Rural charging
4.107
The Victorian Government Department of Environment, Land, Water and
Planning identified that some gaps may emerge in the deployment of public
charging infrastructure particularly in rural and regional parts of the country:
Research has found that the private sector will develop
charging infrastructure at destinations such as shopping centres as there is an
economic benefit. However, the areas less enticing for private investment are
regional areas. A charging network along key regional routes could unlock
tourism and economic development opportunities.
Tourists and residents are more likely to rely on public
charging stations in regional and rural areas. Those living in rural areas
travel further to access services than metropolitan residents, including
education and employment precincts, and do not have as many public transport
options. Vehicle ownership is perceived as more of a necessity for those living
in regional Victoria. Similarly, tourists driving through regional Victoria
need easy access to public charging infrastructure along popular tourist
routes. Fast charging is particularly beneficial for long trips.[151]
Concluding comments
4.108
With increasing global demand for EVs, the Committee has heard that
there are tremendous opportunities for Australian manufacturers. The Committee
notes evidence suggesting that increasing automation will lead to fundamental
changes to the processes and costs of manufacturing opening niches for
Australian industry. The Committee has also heard that the Australian
automotive sector might look differently to the mass manufacturing model of the
past. The sector may choose to identify and play to its strengths, building
specialist componentry, or assembling imported and locally made parts.
4.109
The Committee is encouraged by the companies that it has had heard from
and visited who are at the forefront of the transition to EVs. For example,
Nissan Casting Australia is already making components for EVs that are then
assembled overseas; SEA Electric is fitting EV technology to truck gliders and
has recently announced an expansion into EV bus manufacturing. In addition to
these companies, there is a significant skilled workforce available to migrate
from conventional automotive manufacturing to EVs; and a substantial and
growing automotive research and development capacity.
4.110
Australia has significant reserves of a range of minerals essential to the
production of lithium-ion batteries, the preferred battery type for EVs
currently and into the foreseeable future. A number of large lithium deposits
have been developed with more on the way. The Committee is concerned that
Australia is primarily engaged in the raw material extraction and export which
only captures 0.5 per cent of the lithium value chain. Clearly more of this
value chain can and should be captured by Australian companies.
4.111
Some mining and exploration companies are partnering with international
companies with processing experience as a means to build processing capability.
The Committee has heard that there are currently four lithium battery factories
under development in Darwin, Townsville and Adelaide. These and other similar
developments may provide the catalyst for an increased refining and processing
presence for lithium and other minerals used in battery manufacture. The Committee
is concerned about the likelihood of a surge in end-of-life EV batteries
requiring recycling or repurposing. There is a need to ensure that companies
interested in battery recycling are guided by comprehensive regulatory
frameworks and the latest R&D to minimise any environmental and safety
risks.
4.112
It is clear that the demand for charging infrastructure will continue to
grow in line with EV numbers. Production of charging units and componentry for
both home and public use, and the installation of such equipment is already
providing economic benefits in states such as Queensland and Western Australia.
This is being led by both the private sector and government. Although it is
likely that the private sector will primarily fund public charging
infrastructure in cities, public funding and planning will be required for
highways and regional areas. Government has a role to play in enabling the
private sector to rollout public charging infrastructure to all parts of the
country.
4.113
A targeted approach will ensure that Australian industry optimises its
economic participation in the transition to EVs. The next chapter will examine
a range of possible federal and state government policies that could support
the Australian industry to seize the opportunities associated with
manufacturing EVs.
Navigation: Previous Page | Contents | Next Page