Summary of committee site visits
This appendix contains summaries of the committee's site visits
to Precision Buses (Edinburgh, South Australia); Nissan Casting Plant and SEA
Electric (Dandenong, Victoria); and Tritium (Murrarie, Queensland).
Site visit to Precision Buses workshop,
Edinburgh (South Australia)
Thursday 9 August 2018
Introduction
A sub-committee conducted a site visit to the Precision
Buses workshop at Edinburgh (South Australia) on Thursday 9 August 2018. The
workshop is located in an industrial region of Adelaide that used to host the
Elizabeth motor vehicle manufacturing plant for General Motors Holden.
Senator Tim Storer (Chair) and Senator David Smith participated
in the site visit.
Precision Buses
The subcommittee were welcomed to Precision Buses by its directors,
Mr Christian Reynolds and Mr Dan Marks; and the director of an associated
business, Precision Components, Mr Mat Finch.
The committee were taken on a tour of the workshop which was
described as a mobility and advanced engineering hub. Mr Reynolds explained
that the hub would encourage collaboration between different companies (with
different skillsets and products) that would foster a culture of innovation.
Photo 1: Electric buses
being manufactured at Precision Buses, Edinburgh (SA)
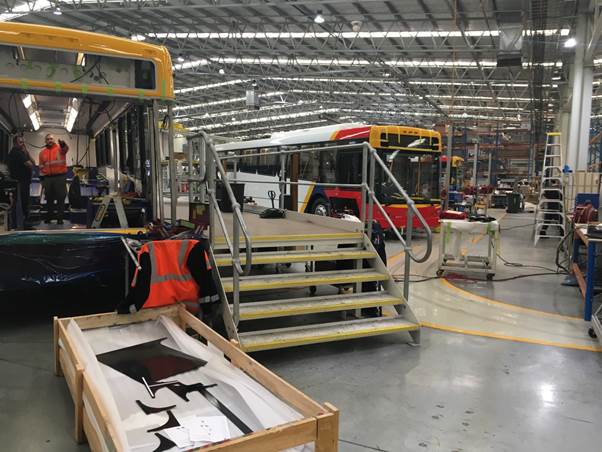
Precision Buses employs 75 employees completing two electric
or low-emissions buses per week. Buses take about eight weeks to assemble from
start to finish. Currently, Precision Buses import and assemble the buses, but
are looking at opportunities to bring more of the manufacturing process
in-house and to business partners here in Australia.
The sub-committee was provided with a demonstration drive in
a fully-electric bus.
Photo 2: Senator Storer
and Senator David Smith inspecting a fully-electric bus prior to the
demonstration

The visit concluded with a presentation on future opportunities
for the company and the sector more broadly. The subcommittee was told that
Precision Buses saw manufacturing electric buses as the first part of journey
to a re-imagined public transport system. Precision Buses view automation,
changed seating arrangements, using buses as work stations as just some of the
changes that could drive increased productivity and enjoyment from commuting
time.
On behalf of the committee, the Chair thanked Precision
Buses for hosting and speaking with the subcommittee.
Site visit to Nissan Casting Plant,
Dandenong (Victoria)
Thursday 30 August 2018
The committee visited the Nissan Casting Australia Plant
(NCAP) in Dandenong on Thursday 30 August 2018. Senator
Storer (Chair), Senator Carr (Deputy Chair), Senator Rice, Senator David Smith
and Senator Patrick participated in the site visit.
The committee were welcomed by Mr Marcus Spindler (General
Manager, NCAP), Mr Stephen Hope (Chief Financial Officer, Nissan Motor Co.
Australia (Nissan)), Mr Balaji Narayana (Operations and Engineering Manager,
Nissan), Mr Wayne Harris (Head of Electrification and Future Mobility, Nissan),
Mr Angus Robinson (Manager, OHE and Quality, Nissan), Mr Brian Cooper (New
Projects Manager, NCAP), and Ms Karla Leach (General Manager, Corporate
Communications, Nissan).
The visit commenced with brief introductions and a short presentation
about NCAP.
The committee was told that NCAP is a high pressure die
casting facility manufacturing over 40 cast aluminium parts for a range of
Nissan vehicles—both internal combustion vehicles and electric vehicles. The
plant has the capacity to cast 10 000 tonnes/annum of aluminium parts and
employs 196 full time equivalents. The 13 die-cast machines have a rated
capacity ranging from 800 tonnes to 2 500 tonnes. The facility also uses
integrated robot fettling and laser marking to finish the casts. The casting
process is then followed by a quality assurance program that ranks the NCAP
facility as one of the highest performing of Nissan's worldwide plants with
respect to minimising part failures.
Photo 3: Completed die
cast vehicle components ready for dispatch at NCAP
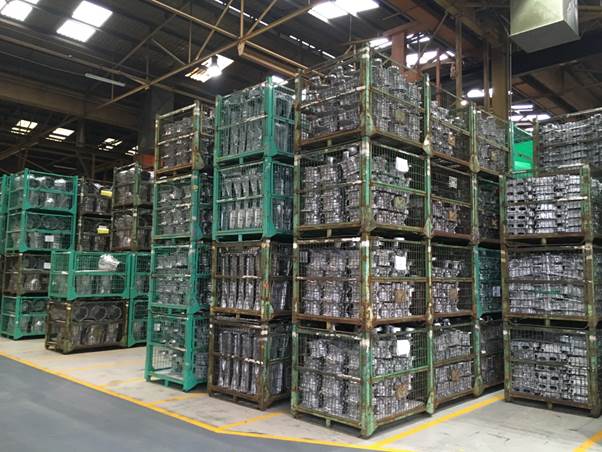
The committee was told that the low rates of failure are
recognised by Nissan's head office as this a critical attribute for electric vehicle
componentry. Currently, NCAP is operating at its capacity and is looking at
ways to increase its production.
Photo 4: Examples of
completed die-cast components
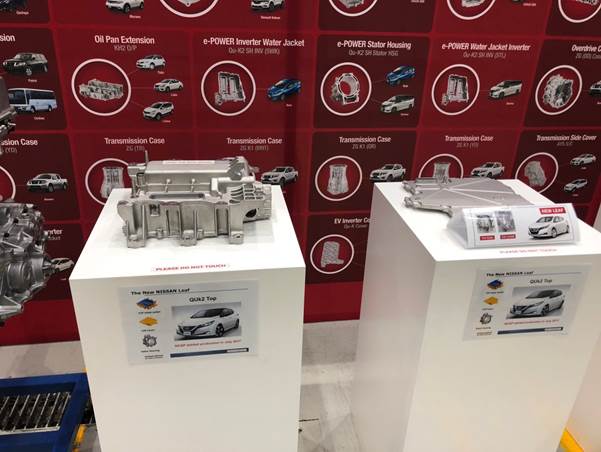
NCAP spoke about the high level of integration that NCAP has
with a large number of local suppliers in the Dandenong area.
The committee was told that the most significant factors for
the future of NCAP were cost-competiveness and quality. Energy costs were also cited
as one of the most challenging attributes in maintaining the cost-competiveness
and profitability of the facility.
The committee was taken on a tour of the plant. At the
conclusion of the tour, committee members thanked NCAP and Nissan for hosting
and speaking with the committee.
Photo 5: Committee members
and NCAP employees at the conclusion of the site visit
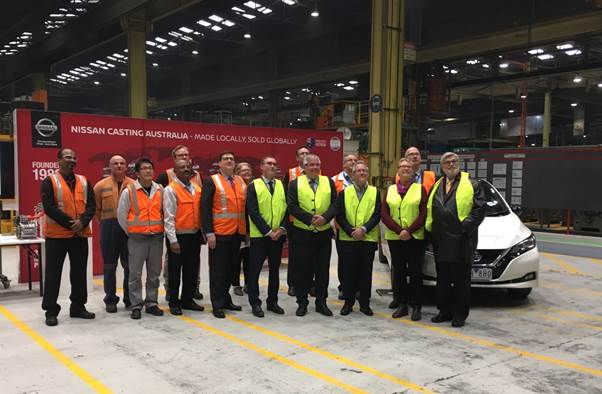
Site visit to SEA Electric, Dandenong
(Victoria)
Thursday 30 August 2018
The committee travelled to SEA Electric at the conclusion of
its visit to NCAP. Senator Storer (Chair), Senator Carr (Deputy Chair), Senator
Rice, Senator David Smith and Senator Patrick participated in the site visit.
The committee was welcomed to SEA Electric by Mr Tony
Fairweather (Chief Executive Officer) and Mr Simon Humphries (Chief Engineer,
Isuzu Australia). The visit commenced with brief introductions and a short
presentation.
The committee was told that SEA Electric currently fits a
range of commercial delivery vehicles with electric powertrains and batteries
(moving to simply fitting electric powertrain and batteries to gliders).[1]
These vehicles would be used for delivering groceries, freight, concrete and
collecting rubbish. These vehicles typically have a daily driving range of up
to 300 kilometres and a regular dwell-time to facilitate battery charging. SEA
claimed that purchase and conversion of these new vehicles are economical in these
vehicle classes with a payback of less than four years.
Photo 6: A number of
gliders being fitted with EV powertrains and batteries in the SEA Electric
workshop
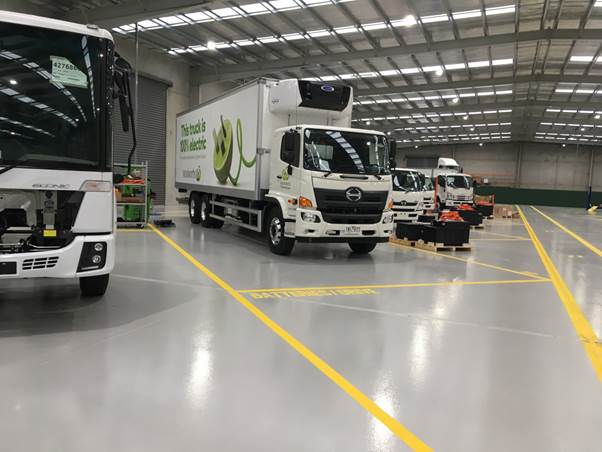
Once the conversions are complete, the committee was told
that each vehicle must undergo a vehicle certification consistent with the
Australian Design Rules including noise and instrumentation assessments, but
not crash testing.
The committee was told that some of the components being
used such as the cooling packs were designed in Australia.
SEA Electric noted that some of the conversion work was
originating from New Zealand. These conversions were funded through the New
Zealand Government Energy and Efficiency and Conservation Authority's Low
Emission Vehicles Contestable Fund.[2]
Mr Fairweather stated that there was an opportunity for
companies such as SEA to retrofit as larger original equipment manufacturers
were not able to dynamically compete with companies like SEA Electric due to a
combination of long lead times for vehicle development and rapid changes in
battery, powertrain and integrator software technology.
One of the challenges in converting internal combustion
vehicles is that EVs are generally heavier due to the weight of batteries.
Typically, the smaller of the vehicles converted are a nominally 4.5 tonne Gross
Vehicle Mass (GVM), which can be driven by a person with a regular car licence.
However, once these vehicles are converted to an EV, the vehicles can exceed
the 4.5 tonne GVM and require a driver to hold a specialist licence class.
The committee was taken on a tour of the workshop and was
taken on a test-drive in one of the converted vehicles. At the conclusion of
the tour, committee members thanked SEA Electric for hosting and speaking with
the committee.
Site visit to Tritium, Murrarie
(Queensland)
Thursday 27 September 2018
Prior to the committee's Brisbane public hearing on Thursday
27 September 2018, the committee conducted a site visit to the Tritium
manufacturing workshop at Murrarie in Brisbane's eastern suburbs. Senator
Storer (Chair), Senator Carr (Deputy Chair), Senator Bushby, Senator Rice,
Senator David Smith and Senator Patrick participated in the site visit.
The committee was welcomed to Tritium by Mr Paul Sernia
(Co-Founder and Chief Product Officer), Mr David Toomey (Head of Corporate
Development) and Mr Nathan Dunlop (Sales and New Market Analyst). Mr
Toomey and Mr Sernia provided the committee with a brief overview of the
company which manufactures public chargers and the broader sector.
Photo 7: Committee members
and tritium employees in front of some of the EV chargers manufactured by
Tritium
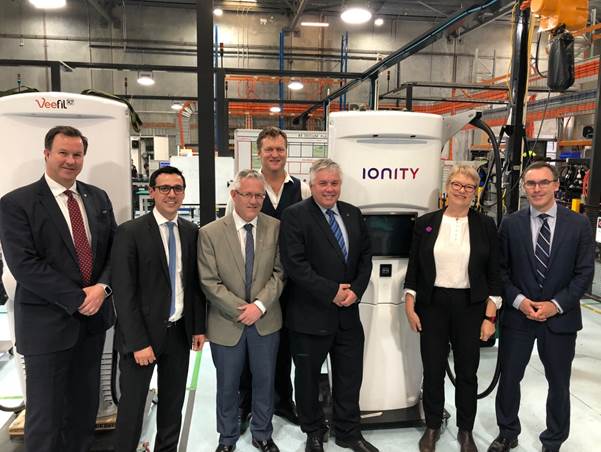
Mr Sernia informed the committee that Tritium was founded
about 20 years ago and started out building components for EVs. In more recent
years, it has moved to manufacturing public charging infrastructure that is
largely being rolled out in mature European EV markets such as Norway. The
company has increased its workforce from 58 employees (2016) to 254 (2018) with
the vast majority of these employees in Australia (229). Tritium also has
offices in the United States (15 employees) and the European Union (10). A
little over half of the employees are involved in manufacturing (98) with a
slightly smaller number conducting research and development.
The committee were told that Tritium's ethos is clean,
healthy and convenient cities with a focus on providing energy freedom. Tritium
has a specific emphasis on transportation and energy storage solutions
associated with using EVs. The company manufactures three different models
which range from slow charging to fast (and why the prices varied accordingly).
Mr Sernia said that work is being undertaken on ultra-fast chargers to bring
charging time down from 20 minutes to a 5–10 minute charge time.
Mr Sernia described some of the unique characteristics of
Tritium's charging equipment including that it is compact enough to fit into
smaller spaces such as narrow pathways. Mr Toomey stated that the charger's compact
design is aided by a liquid cooled design which is different to the air-cooled
models developed by a number of competitors. Intellectual property generation
is an important aspect of the business (about half of Tritium's engineers are
software engineers). Tritium meets regularly with EV manufacturers to ensure
that Tritium's technology is able to 'talk' or communicate to many different
types of EVs.
Photo 8: The workshop floor at Tritium
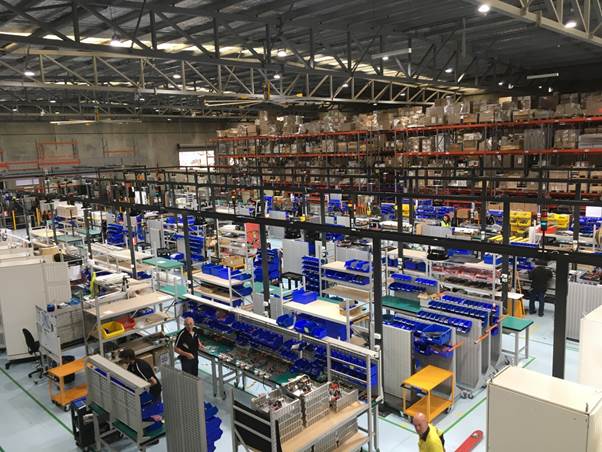
The committee discussed a range of opportunities and
challenges related to EVs and public charging infrastructure before taking a
tour of the workshop. Committee members thanked Tritium for hosting and
speaking with the committee.
Navigation: Previous Page | Contents